Om oss
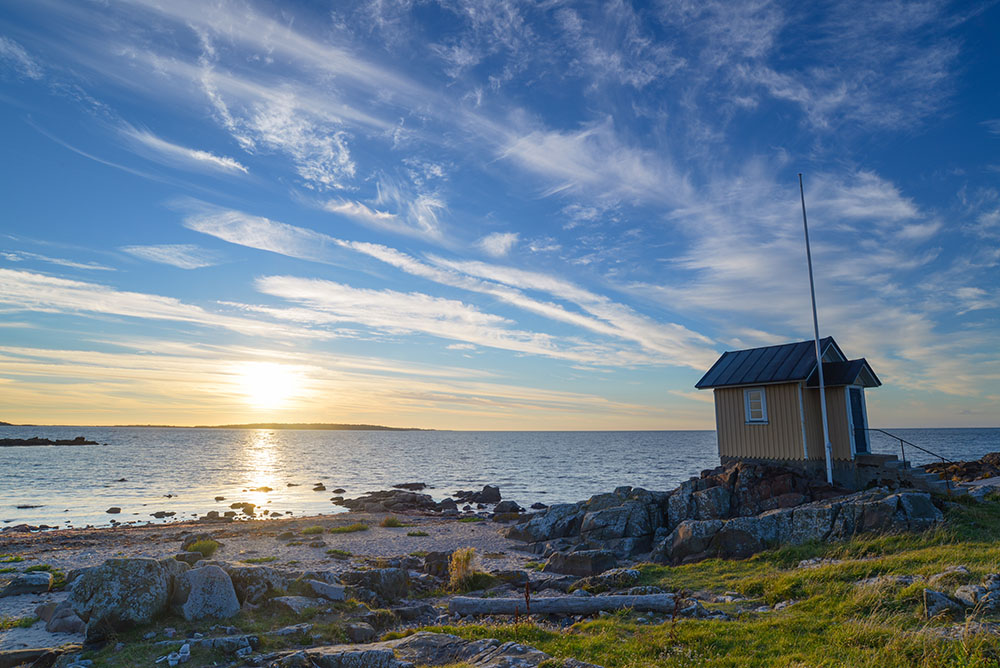
Isakssons Gummifabrik AB grundades 1949 av Emil, Ester & Börje Isaksson, och drivs idag av Christer Isaksson & Ronny Fengved i tredje generationen, i samarbete med den fjärde generationens Isaksson, Hansson & Fengved.
Isakssons Gummifabrik AB erbjuder produkter av naturgummi till tandvård, sjukvård och tillverkningsindustri. Vårt uppdrag är att tillhandahålla funktionella, användarvänliga och säkra produkter som håller hög kvalité, samt tillverkas med väl prövade metoder. Vårt fokus är att odla långsiktiga relationer med våra kunder genom att erbjuda produkter som ger ett mervärde för slutanvändaren.
Vi är ett företag som består av drivna och branschkunniga personer i blandade åldrar med mångårig samlad erfarenhet.
Isakssons Gummifabrik AB har både huvudkontor och tillverkning utanför Torekov i Båstads Kommun, med kunder i Sverige, Europa, Asien, Nord- & Sydamerika. Vi är registrerade hos det Svenska läkemedelsverket och är certifierade enligt ISO 13485.
Övergripande historik
Isakssons Gummifabrik AB, som är placerad i Båstad kommun, i närheten av Torekov, bär på en drygt 85-årig historia. Verksamheten har präglats av finurliga tekniska lösningar, internationell lansering, slumpmässiga händelser som lett till nya produkter, samt en ständig utveckling och förbättring av tillverkningen.
1931 startade målaren Emil Isaksson tillsammans med skomakarna Edvin Isaksson och Martin Paulsson Firma Rågummiindustri. Företaget tillverkade stövlar i rågummi, en innovation som också beviljades patent. Förmodligen var detta Sveriges första patent på gummiprodukter. Behovet av tåliga stövlar hade uppstått vid arbete med byggnationer i Torekovs hamn.
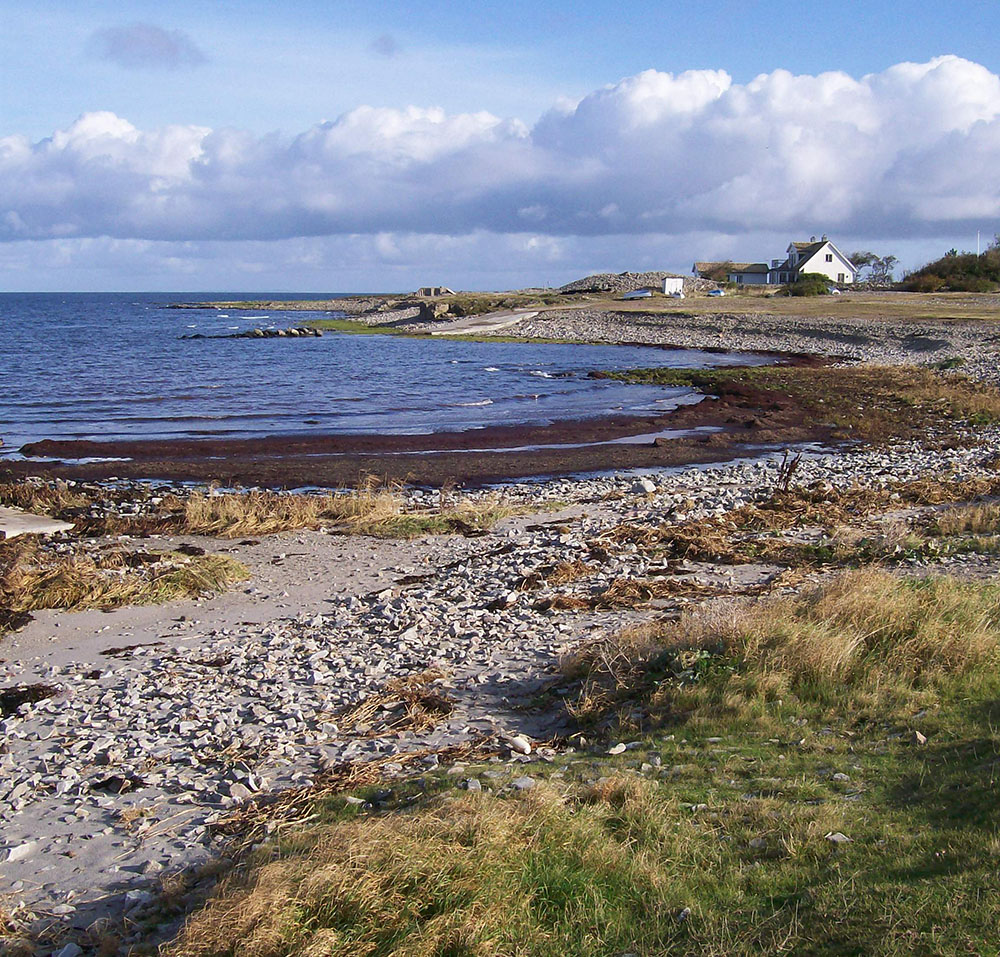
Det nya företaget engagerade många i Torekov. Såväl arbetskraft som beställningar på stövlar strömmade in. Först skedde produktionen i Emil Isakssons fastighet i Varan, Torekov och grannar och bekanta bidrog i arbetet med att inreda lokalerna.
Detta var dock bara ett provisorium i företagets inledningsskede. En tomt för en större fabrikslokal fanns redan inköpt. Byggmästaren Carl Ekensteen ledde bygget och i december 1931 flyttade verksamheten in i den nybyggda fabriken.
Redan från början visades intresse från utlandet. En dansk ingenjör ville starta tillverkning av gummistövlar och en delegation från Firma Rågummiindustri tillbringade några månader i Danmark för att utbilda personal.
Några år in på 1930-talet försämrades marknaden genom den ekonomiska depressionen. Sven Boström och Bernhard Jorlén – som båda arbetade på kontoret – tog 1938 över verksamheten och skapade Nordiska Latexfabriken (numera Nolato). Emil Isaksson arbetade vidare som teknisk chef på det rekonstruerade företaget; han utvecklade tekniken – såväl kring latex som fastgummi – och skapade därmed en kontinuitet för gummitillverkningen i Torekov.
Under åren före andra världskriget var tröstnappar och dinappar två av Nordiska Latexfabrikens största produkter. En dansk ingenjör vid namn Andersén, specialist på doppade produkter i naturlatex, tog fram gummimassan för tillverkningen och utbildade Emil Isaksson, Sven Boström och övrig personal i latexhantering. Napparna såldes under varunamnet ”Stilles vita napp”.
Under andra världskriget var det dock helt omöjligt att importera naturlatex. Förutsättningen för att kunna fortsätta produktionen av nappar var att man hade tillgång till gummimassa i flytande form. Emil Isaksson och Sven Boström började experimentera med detta och fick fram en solution som gick att använda för att producera doppade artiklar. Den tekniska lösningen var en variant av återvinning. Isaksson och Boström lyckades utvinna gummimassa ur rågummi. Företaget köpte upp gamla rågummidetaljer, inte minst kasserade rågummistövlar och använde materialet för tillverkning av gummimassa. Ett exempel så gott som något på kreativ mentalitet. Men hanteringen och tillverkningsprocessen var knappast hälsosam, framför allt inte utifrån dagens regelverk. Rågummit löstes upp med hjälp av bensen och trikloretylen, lösningsmedel som idag omges av rigorösa bestämmelser, men som då användes flitigt och helt utan skyddsåtgärder.
För att inhämta kunskap om tekniken kring fastgummi köpte ledningen på Nordiska Latex i början av 1940-talet in sig i Trönninge Gummifabriks AB (numera National Gummi AB) utanför Halmstad. Under två år arbetade Emil Isaksson i Trönninge för att förkovra sig i fastgummihantering. Under dessa två år visade han också sin ständigt kreativa sida genom att utveckla maskinparken och tillverkningsmetoderna vid fabriken i Trönninge.
1949 lämnade Emil Isaksson Nordiska Latexfabriken och grundade Isakssons Gummifabrik i sin och hustrun Esters fastighet, där stöveltillverkningen startat 1931. I verksamheten arbetade Emil, Ester och sonen Börje. Det nuvarande företaget, Isakssons Gummifabrik AB, ligger fortfarande kvar på samma plats, nu i större och moderna lokaler. Senaste utbyggnaden av lokaler skedde på 1980-talet. Under efterkrigstiden fanns en nyvaknad marknad för gummileksaker. Sagt och gjort! Det nya företaget utvecklade tekniska lösningar och började tillverka ihåliga dockor i naturlatex. En stor kund var varuhuskedjan EPA. Men efter några år blev konkurrensen, framför allt från Tjeckoslovakien och Japan, alltför hård. Det gällde alltså att ta fram nya produkter.
Genom slump, kreativitet och experimenterande startade nu utvecklingen av det som fortfarande är företagets dominerande produkt, kofferdam, den tunna och mycket elastiska gummiduk som används av tandläkare, bland annat vid rotfyllning. Under de dryga 60 år som gått sedan gummiduken först togs fram har receptet på gummiblandningen samt tillverkningsprocessen förändrats och förbättrats och kvalitén har därmed ytterligare förfinats.
Snart var det dags för ytterligare en av företagets centrala gummidetaljer, ”Original-von Rosen-skenan”, konstruerad av ortopedläkaren Sophus von Rosen. Skenan används vid behandling av medfödd höftledsluxation hos nyfödda barn och har sedan 1957 tillverkats och vidareutvecklats av Isakssons Gummifabrik. Sedan 1975 tillverkas hela produkten under varunamnet ”Original-von Rosen-skenan”, såväl aluminiumkärnan, bolstringen och överdraget av Isakssons Gummifabrik AB. Tillverkningen sker enligt detaljerade bestämmelser angående skenans uppbyggnad. Bestämmelserna togs fram i samarbete mellan Sophus von Rosen, Isakssons Gummifabrik AB och det aktiva läkarlaget på Ortopediska kliniken vid MAS i Malmö (numera SUS), med biträdande överläkaren Lars Danielsson i spetsen.
En tredje epokgörande produkt – Bresle Patch – togs fram i mitten av 1990-talet. Civilingenjör Åke Bresle på dåvarande Sveriges Provnings- och Forskningsinstitut, (nu under namnet SP Sveriges Tekniska Forskningsinstitut, tidigare Statens Provningsanstalt) sökte efter en gummiduk, där kraven på rivhållfasthet och renhet var extremt höga. Inga av de dukar han provat uppfyllde kraven, varken på rivhållfasthet eller renhet. Åke Bresle tog kontakt med Isakssons. Denna kontakt ledde vidare och i juni 1996 skrevs ett avtal mellan Isakssons Gummifabrik AB och Sveriges Provnings- och Forskningsinstitut. Isakssons har därefter utvecklat produktionen.
Produkten Bresle Patch används genom att konduktiviteten (ledningsförmågan) mäts och på så vis spåras salter och föroreningar som inte är synliga för ögat, men som kan få allvarliga konsekvenser. Bland annat undersöks risken för rostangrepp på broar som behandlats med vägsalt. Andra användningsområden kan vara att spåra föroreningar efter bränder eller föroreningar på ytor som ska målas, till exempel fartygsskrov.Produkten Bresle Patch används genom att konduktiviteten (ledningsförmågan) mäts och på så vis spåras salter och föroreningar som inte är synliga för ögat, men som kan få allvarliga konsekvenser. Bland annat undersöks risken för rostangrepp på broar som behandlats med vägsalt. Andra användningsområden kan vara att spåra föroreningar efter bränder eller föroreningar på ytor som ska målas, till exempel fartygsskrov.
Mätningen sker genom att Bresle Patch placeras på materialet som ska undersökas. En injektionsnål sticks genom gummiduken, destillerat vatten sprutas in och sugs därefter ut igen för att analyseras.Sedan dess tillverkar Isakssons gummiduken som levereras till SP Sveriges Tekniska Forskningsinstitut.
En bandagemästare, en gummihandske och Original-von Rosen-skenan
I mitten av 1950-talet konstruerade bandagemästaren (numera är titeln ortopedtekniker) Curt Petersson en protes i form av en rörlig hand, med en för den tiden avancerad mekanik. Curt Petersson var verksam på bandageverkstaden vid ortopediska kliniken på Lunds Lasarett. Protesen var funktionell, men han ville också att den skulle se så naturtrogen ut som möjligt. En släkting till Curt Petersson bodde granne med Isakssons Gummifabrik och på det viset knöts en kontakt mellan Curt och Isakssons. Efter lite dividerande och experimenterande tillverkade Isakssons en gummihandske till protesen. Handsken gick nästan inte att skilja från en riktig hand.
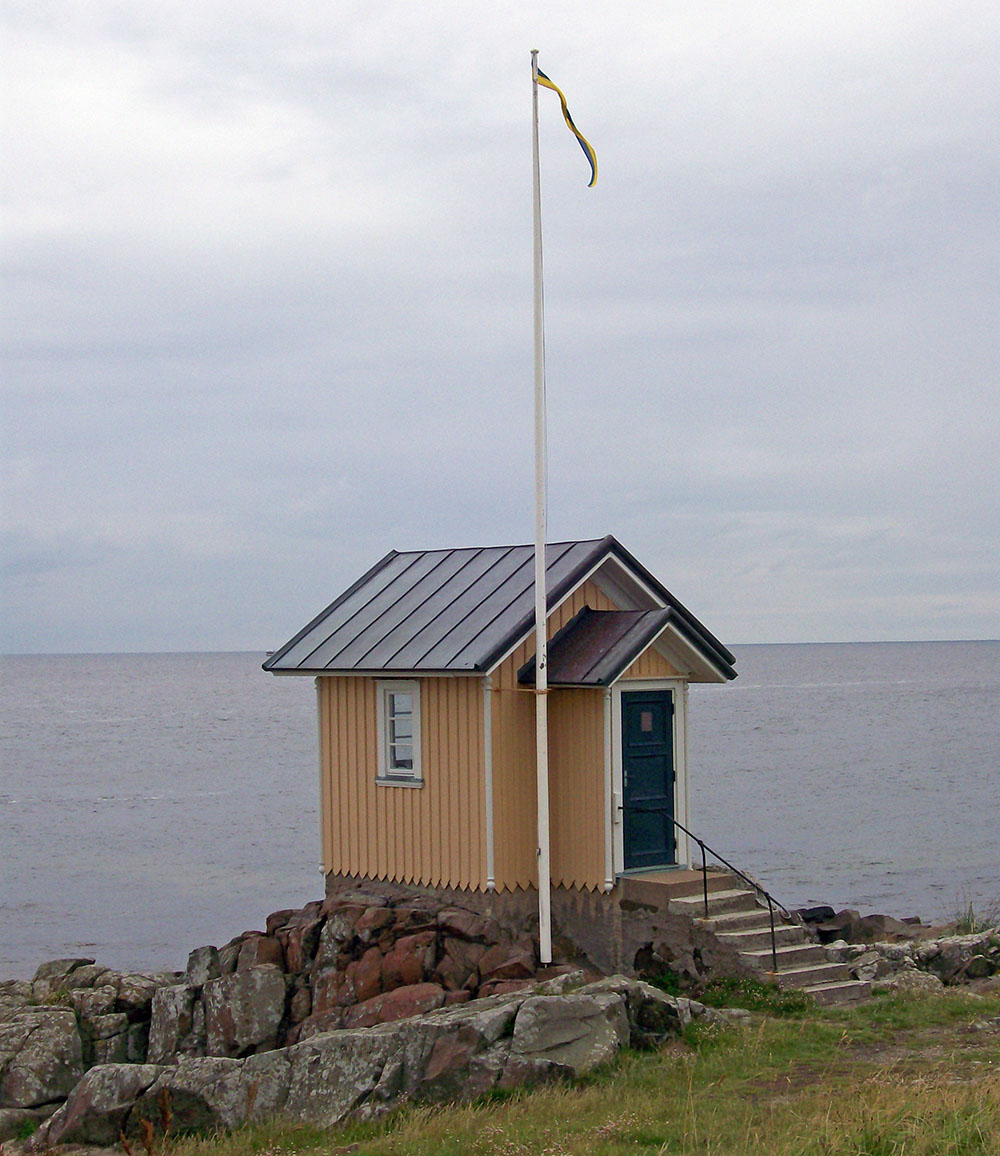
En tid därefter konstruerade Sophus von Rosen det som skulle bli Original-von Rosen-skenan, som används för att behandla nyfödda med medfödd höftledsluxation. von Rosen var överläkare vid ortopediska klniken på dåvarande Malmö Allmänna Sjukhus. och han sökte efter ett lämpligt material för att klä in skenan och därmed förhindra föroreningar från urin och avföring.
von Rosen diskuterade frågan med bandgagemästarna och Curt Petersson visade honom handsken som tillverkats av Isakssons. Sophus von Rosen blev omedelbart intresserad. Dessutom visade det sig att von Rosen hade sommarhus i Torekov och sommaren 1957 sammanstrålade Emil och Börje Isaksson, Curt Petersson och Sophus von Rosen i Torekov.
Resultatet av detta första möte blev att Isakssons Gummifabrik började tillverka prototyper till gummiöverdrag för skenan, medan skenans innerdelar, skumplaststoppningen och aluminiumkärnan, tillverkades på bandageverkstaden vid Malmö Allmänna Sjukhus.
Efterhand började det dock komma ut dåliga kopior av skenan på marknaden. Därför togs 1975 detaljerade bestämmelser angående skenans uppbyggnad fram i samarbete mellan Sophus von Rosen, Isakssons Gummifabrik AB och det aktiva läkarlaget på Ortopediska kliniken vid MAS i Malmö, med biträdande överläkaren Lars Danielsson i spetsen. I bestämmelserna stipulerades exakta regler om hur skenan skulle byggas upp. Sedan 1975 tillverkas hela produkten under varunamnet Original-von Rosen-skenan, såväl aluminiumkärnan, bolstringen och överdraget av Isakssons Gummifabrik AB. I samband med en internationell ortopedkongress i Lund 1975 visade också Isakssons fram slutresultatet.
Original-von Rosen-skenan har behandlats i tre vetenskapliga avhandlingar, av läkarna Nis Fredensborg (1975), Kurt Palmén (1961) och Göran Hansson (1980).
Historien bakom kofferdam
Slumpen och kreativt experimenterande – historien bakom kofferdam
Två resande försäljare möts på ett hotell. Det blir starten på utvecklingen av kofferdam, det som idag är huvudprodukten från Isakssons Gummifabrik AB.
Emil Isakssons svåger, Erik Stefansson, arbetade som resande försäljare. I början på 1950-talet mötte han på ett hotell en försäljare från Dentalaktiebolaget. Denne visade honom en bit gummiduk. Det var kofferdam, gummiduk som används av tandläkare, bland annat vid rotfyllningar. Duken tillverkades i USA, men Dentalaktiebolaget hade utan framgång försökt få nordisk gummiindustri att vidareutveckla produkten. Ingen fabrik hade visat intresse för detta.
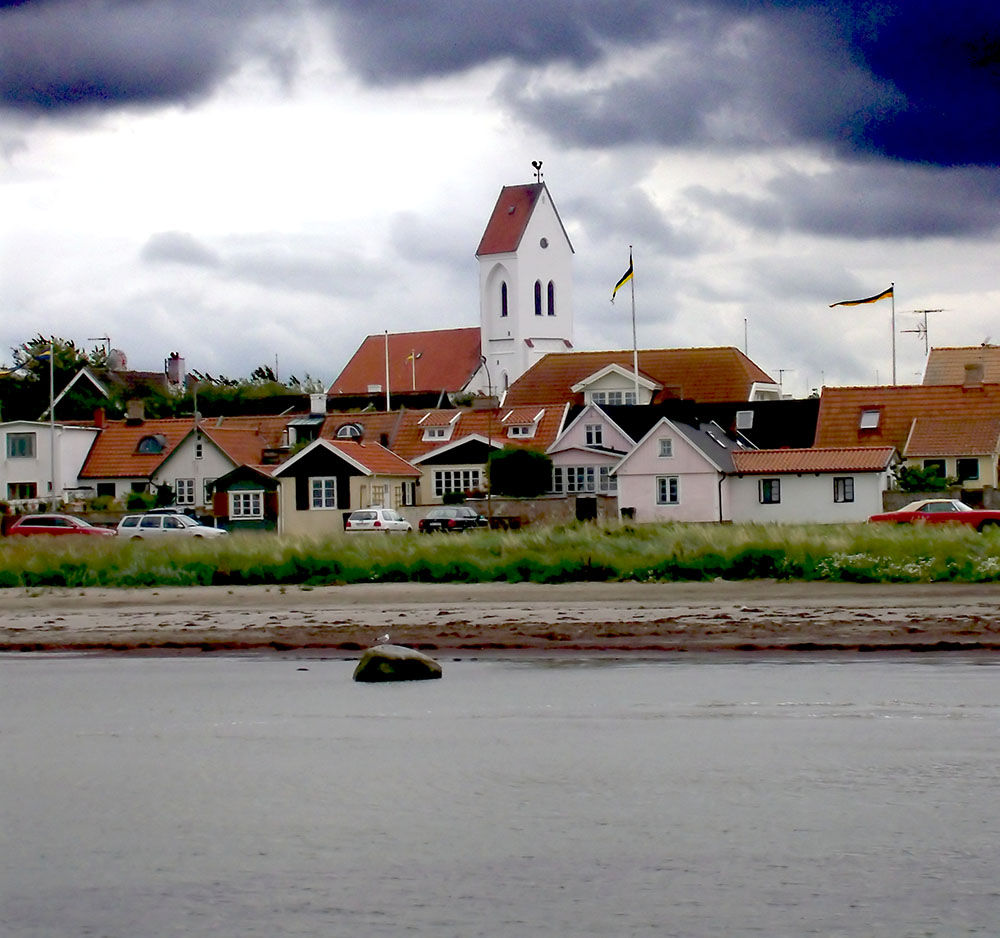
En tid senare var Erik Stefansson på besök hos Emil och Ester Isaksson. Han berättade om gummiduken som försäljaren från Dentalaktiebolaget hade visat. Utan ett ord reser sig Emil och går ut till fabriken. En stund senare kommer han tillbaka med en bit gummiduk i handen.
– Är det en sån här du menar?, frågade Emil. Erik stirrade och nickade. Här fanns en prototyp till det som Dentalaktiebolaget efterfrågade! I hemlighet hade Emil experimenterat och ur flytande gummi lyckats skapa en tunn och mycket elastisk gummiduk. Men för Emil var det bara ett experiment. Var det något som kunde användas? I så fall – till vad?
Erik Stefansson tog med sig en bit gummiduk och kontaktade disponent Uno Feldt på Dentalaktiebolaget. Resultatet blev att Dentalaktiebolaget snabbt svarade Isakssons Gummifabrik och ville diskutera utveckling av materialet.
Sommaren 1952 skrevs ett avtal mellan Dentalaktiebolaget och Isakssons Gummifabrik. Men för produktion i större skala fanns det inga metoder och inga maskiner. Återigen visar sig kreativiteten hos Isakssons. Experimenten fortsätter, produktionsmetoder och material utvecklas och efterhand börjar leveranserna av kofferdam till Dentalaktiebolaget.
Idag är produktionsmetoder och teknik vidareutvecklade och delvis annorlunda, men gummiduken är grunden i verksamheten och kofferdam är den dominerande produkten från Isakssons Gummifabrik. Cirka 80% av produktionen går på export till ett femtontal länder, bland annat Japan, Kanada, USA, Tyskland och våra nordiska grannländer.
Bresle Patch
Bresle Patchen togs fram i mitten av 1990-talet. Civilingenjör Åke Bresle på dåvarande Sveriges Provnings- och Forskningsinstitut, (nu under namnet RISE, tidigare SP Sveriges Tekniska Forskningsinstitut, och dessförinnan Statens Provningsanstalt) sökte efter en gummiduk, där kraven på töjbarhet, rivhållfasthet och renhet var extremt höga. Inga av de dukar han provat från andra tillverkare uppfyllde kraven på varken rivhållfasthet eller renhet.
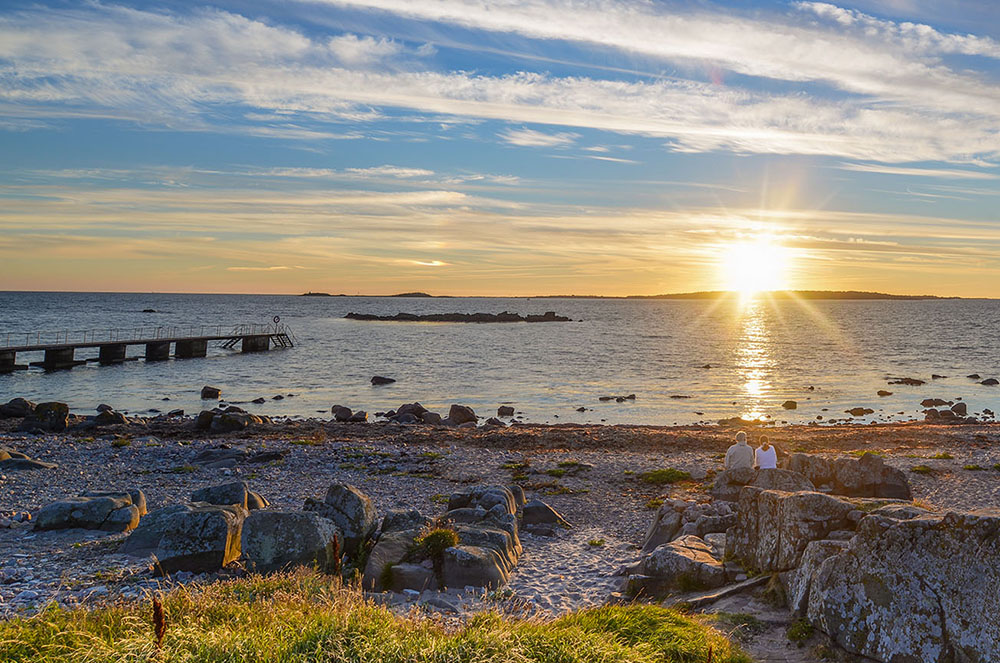
Åke Bresle tog därför kontakt med Isakssons, och tillsammans utvecklade de metoder för att tillverka en gummiduk som dels bibehöll den töjbarhet och rivhållfasthet som Isakssons gummiduk redan hade, men även kunde möta renhetskraven. 1996 skrevs avtal mellan Isakssons Gummifabrik AB och Sveriges Provnings- och Forskningsinstitut, och sedan dess tillverkar Isakssons den gummiduk som används i Bresle-patchen.
Produkten Bresle Patch används genom att konduktiviteten mäts och på så vis spåras salter och föroreningar som inte är synliga för ögat, men som kan få allvarliga konsekvenser. Bland annat undersöks risken för rostangrepp på broar som behandlats med vägsalt. Andra användningsområden kan vara att spåra föroreningar efter bränder eller föroreningar på ytor som ska målas, till exempel fartygsskrov.
Mätningen sker genom att Bresle Patch placeras på materialet som ska undersökas. En injektionsnål sticks genom gummiduken, destillerat vatten sprutas in och sugs därefter ut igen för att analyseras.
Kunder
Dental DAM
Gummiduk
Research Institutes of Sweden
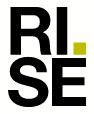
Becton Dickinson
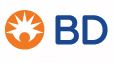
Nordic Plastics Group

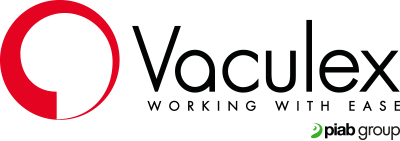
Sveriges Tekniska Forskningsinstitut
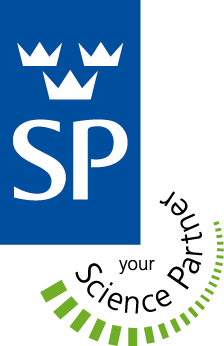
Helsingborgs Gummifabrik AB
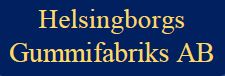
Ortopedi Sverige
Aktiv Ortopedteknik
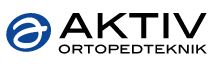
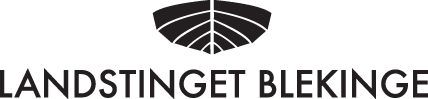
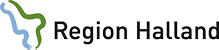
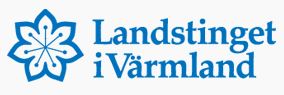

Höglandssjukhuset Eksjö & Nässjö
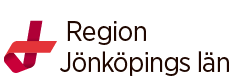
Karolinska Universitetssjukhuset
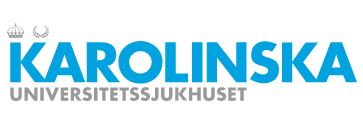
Norra Älvsborgs Sjukhus
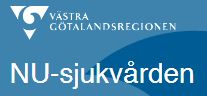
Norrlands Universitetssjukhus
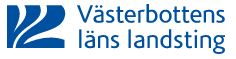
Ryhov, Region Jönköping
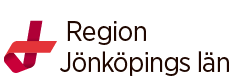
Sahlgrenska Universitetssjukhuset

Skaraborgs Ortopedservice, Skövde

Skånes Universitetssjukhus i Malmö och Lund
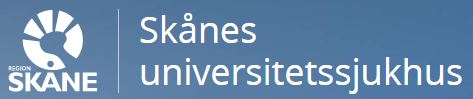
Sundsvalls Länssjukhus
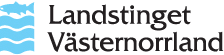
Södra Älvsborgs Sjukhus

Team Olmed
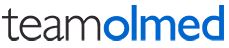
Universitetssjukhuset Linköping

Västerviks Sjukhus
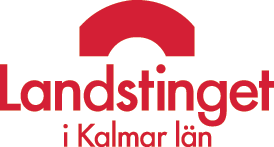
Ortopedi Internationellt
Landspítali Reykjavik, Iceland
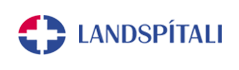
Klaksvíkar Sjúkrahús, Faroe Islands
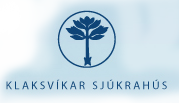
Promedics, UK
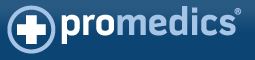
Vasa Centralsjukhus, Finland
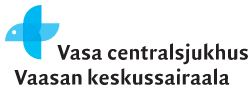
Oy Medisana

NHS Oxford University Hospitals – Nuffield Orthopaedic Centre, UK

NHS Lothian, UK
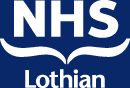
NHS Chelsea & Westminster, UK

Duke University Hospital, Center for Orthotic & Prosthetic Care, USA
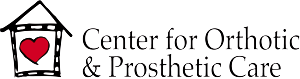
Prothotic Laboratories, USA

Seacoast Orthopedics, USA
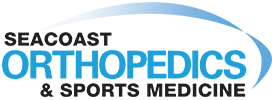
Isakssons Gummifabrik AB
Org. nr: 556062-7217
VAT: SE556062721701
GDPR - Integritetspolicy
Adress: Ängalagsvägen 226
269 95 Båstad, Sweden
GLN: 735001320004
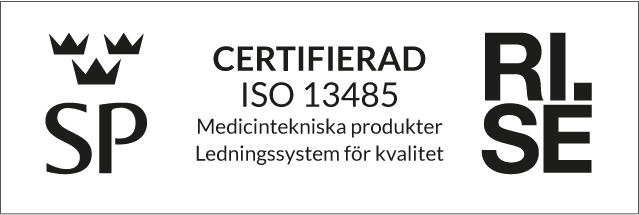